Measure overall machine effectiveness – OEE (Overall Equipment Effectiveness)
OEE or overall equipment efficiency, if we translate directly, “measure the overall efficiency of the machine” OEE is the TPM (Overall Productive Maintenance) goal formulated by Seiichi Nakajima in 1928. Continuously improve the production quality of each industrial activity.
OEE is the overall productivity or production capacity of a factory or production unit. If OEE is 100% The production efficiency of industrial plants is very high. There are no mistakes in terms of availability, production speed and product quality. (However, according to international standards, the benchmark mark is about 85%.)
The relationship is:
OEE=Availability x Performance x Quality
The loss in the variable will reduce OEE if it is shown in the chart.
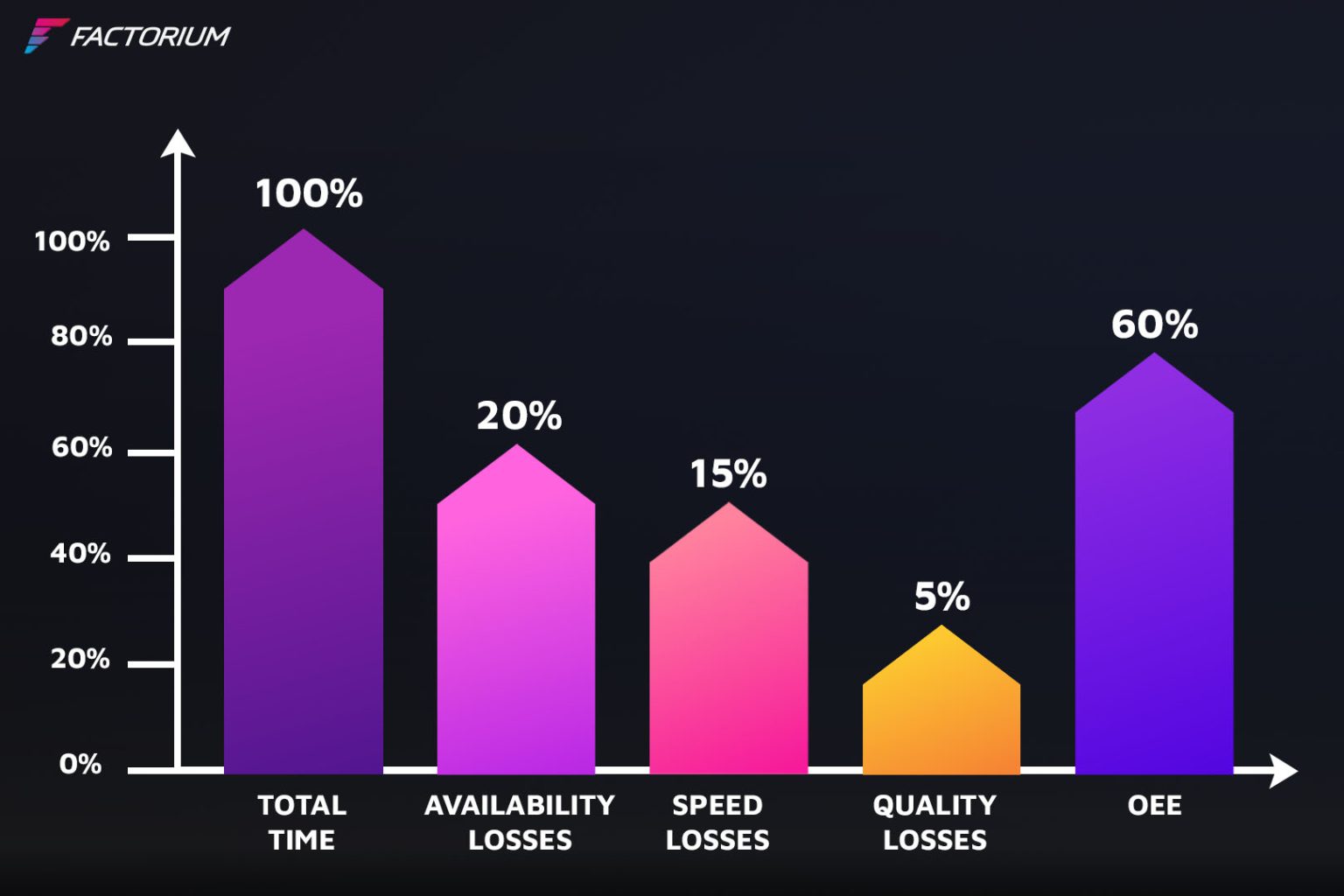
Components of OEE
In measuring OEE from the equation above, there are 3 main components:
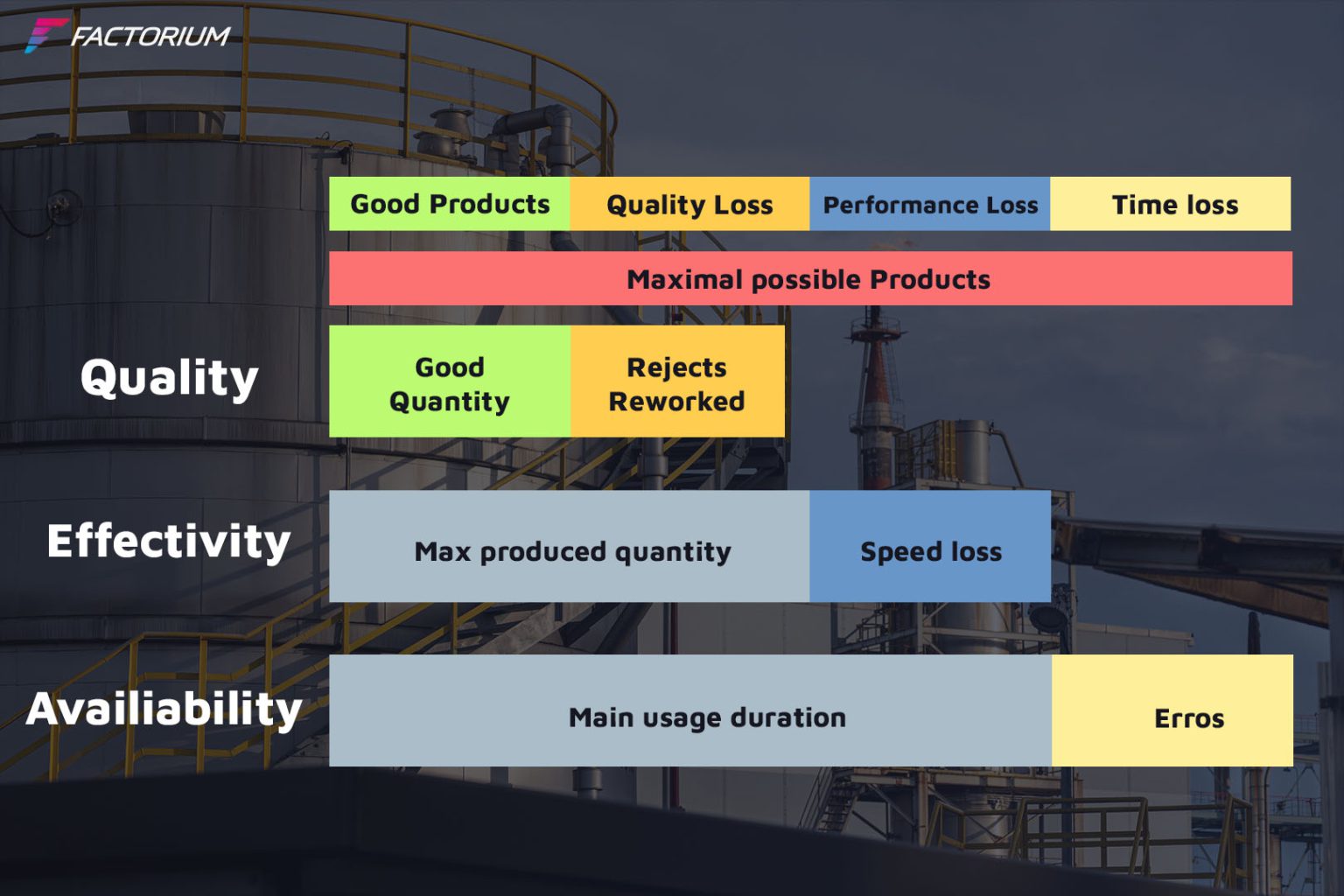
1. The availability or availability of the machine compared with the production plan of the production unit.
If it cannot produce or loses production capacity, it is called “availability loss”.
Or it can be calculated in the following way:
Availability=run time/scheduled time
Availability=performance, machine availability
Operation time=machine operation time
Planned time=planned time to run the machine in the factory
2. Performance or production efficiency can be called process rate. Compared with the designed production speed, how much can the production unit produce?
In the case of design delay, we call it “speed loss”
Or it can be calculated in the following way:
Performance=actual speed/design speed
Performance=productivity
Actual speed=actual production time
Design speed=design time
3. Product quality or quality indicates product quality. According to the factory’s QA/QC system. What is the percentage of quality products?
“Quality loss” is called “quality loss”.
Quality=(unit production – defect unit)/(unit production)
Quality=product quality
Production unit=quality unit
Defect unit=quantity of poor quality
Unit production=total quantity
Benefits of OEE in the factory
In the past, there were many methods for the production capacity of the factory, most of which were production, maintenance, accounting and indicator information. KPI is full, but none of them can be judged as a whole, and none of them can be used to improve productivity.
By measuring the overall efficiency of the machine or using OEE. This is a good way to understand not only the efficiency of the machine, but also the cause of the loss as a whole. It is able to classify the loss and the details of the cause, so that it can correctly and systematically reduce the loss. Just like we drive, there is an instrument that always reminds us whether the factory production is good or bad. This can make the factory really focus on improvement and development.
Increasing the overall productivity of the machine
The main reason for the sharp decline in OEE is the poor condition of the machine, which is also the case in the worst case. It is necessary to stop production to repair the machine. After that, of course, the OEE value of friends will “plummet”.
The first way to prevent these events is to improve the maintenance management system from the old system to the CMMS system, because the CMMS system. Record the history of degradation, wear or frequent failures. It is used to analyze and plan the maintenance work suitable for each type of machine to prevent the machine from frequent damage. Or the use efficiency will directly affect OEE.